Cyber security of our robots and data management systems has the highest priority. We give advice to our customers on how to use the system best. For example: using the system only for business purposes and not for private purposes. Of course, the farmer also has a responsibility in securing his or her data.
Peter: ‘Of course it’s on our minds. After all, we all get things like phishing messages. But I’ve been giving it more thought recently since my insurance company called and mentioned this subject. It made me realise that criminals can do malicious things that can shut your whole company down. I immediately called Ronald Pieterse, who handles IT matters for our farm. Ruud: ‘I used to find it a little annoying that you had to go through several verification steps before you could log in to our system. But now you hear about so many companies getting attacked. So you understand how important it is, and you learn to appreciate the verification procedure.’
This magazine is about cyber security. Is the topic of cyber security on your mind in the context of your farm activities?
Ruud: ‘As a Test & Service Engineer, I bridge the gap between the farmer and the engineers at the office. Peter and Margo can call me if something is wrong, and I make sure the engineers receive this feedback. I also represent the service engineers worldwide. I give feedback on whether a product is easy to service, when commercially released. I have the most diverse job within Lely, I think! One day I will be doing maintenance or solving disruptions, the next day I might be pouring concrete at a farm, I tackle IT tasks, I do the planning for our department and I work on new ideas. I’ve been visiting Peter and Margo’s farm for a few years now. They are friendly and enthusiastic. Peter is really interested in the technology, which is important. He’s also very motivated, so their contribution is very valuable to us.’
Peter: ‘Whenever I call, I know my information will be passed on within Lely, and I always get feedback on what they did with my input. That’s crucial in a relationship with a test farm. I like improving things; when everything is running smoothly, I get bored.’
What is your role on the farm of Peter and Margo?
Peter: ‘As a test farm, you work with the Lely engineers much more intensively; you really get to know each other very well, including on a personal level. The whole relationship is built on trust. I know I can reach out to them whenever a disruption occurs, day or night. The Lely Industries team are so involved with their product and have such a huge sense of responsibility that they never mind. I have never seen employees so committed to their work; Lely should really cherish those people. And as a test farmer, you have to be committed too, and always alert. Disruptions can occur regularly, even in the middle of the night, and you have to take photos or film the alarm. Then, you have to log what you did to solve the issue. You suggest improvements and report malfunctions. If one engineer says it’s not possible to fix something, you need to convince them of the need for it to work. Eventually, there’s always an engineer who manages to find a solution. And the moment when something finally works properly is very fulfilling.’
Ruud Aarts, one of the Lely Test Engineers and working closely with Peter and Margo: ‘Remember that a lot of today’s engineers don’t actually have an agricultural background. Our farmers are their eyes and ears for the development work being done in the office.’
What’s the difference between being a Lely customer and being a Lely test farm?
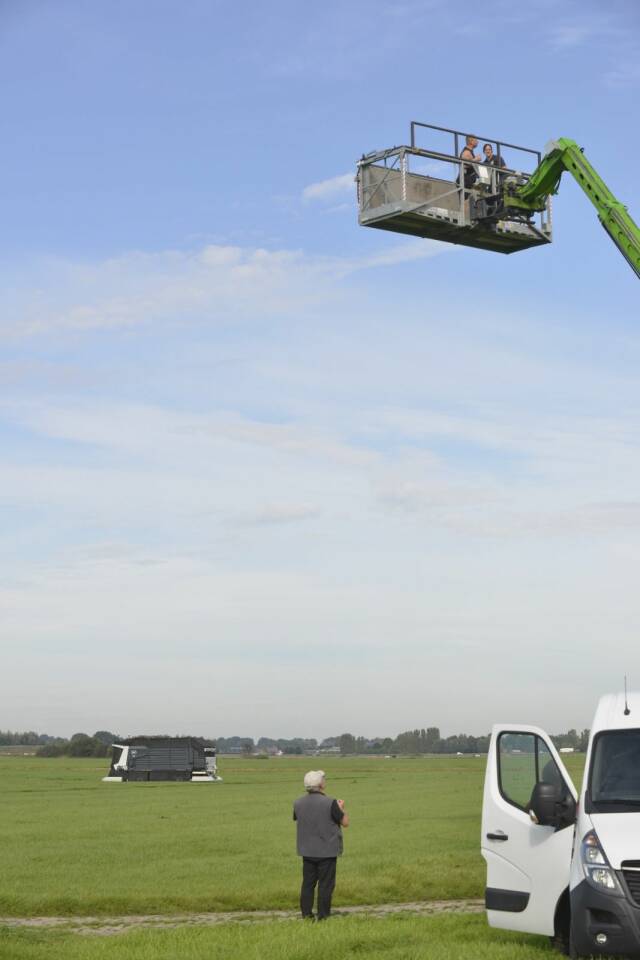
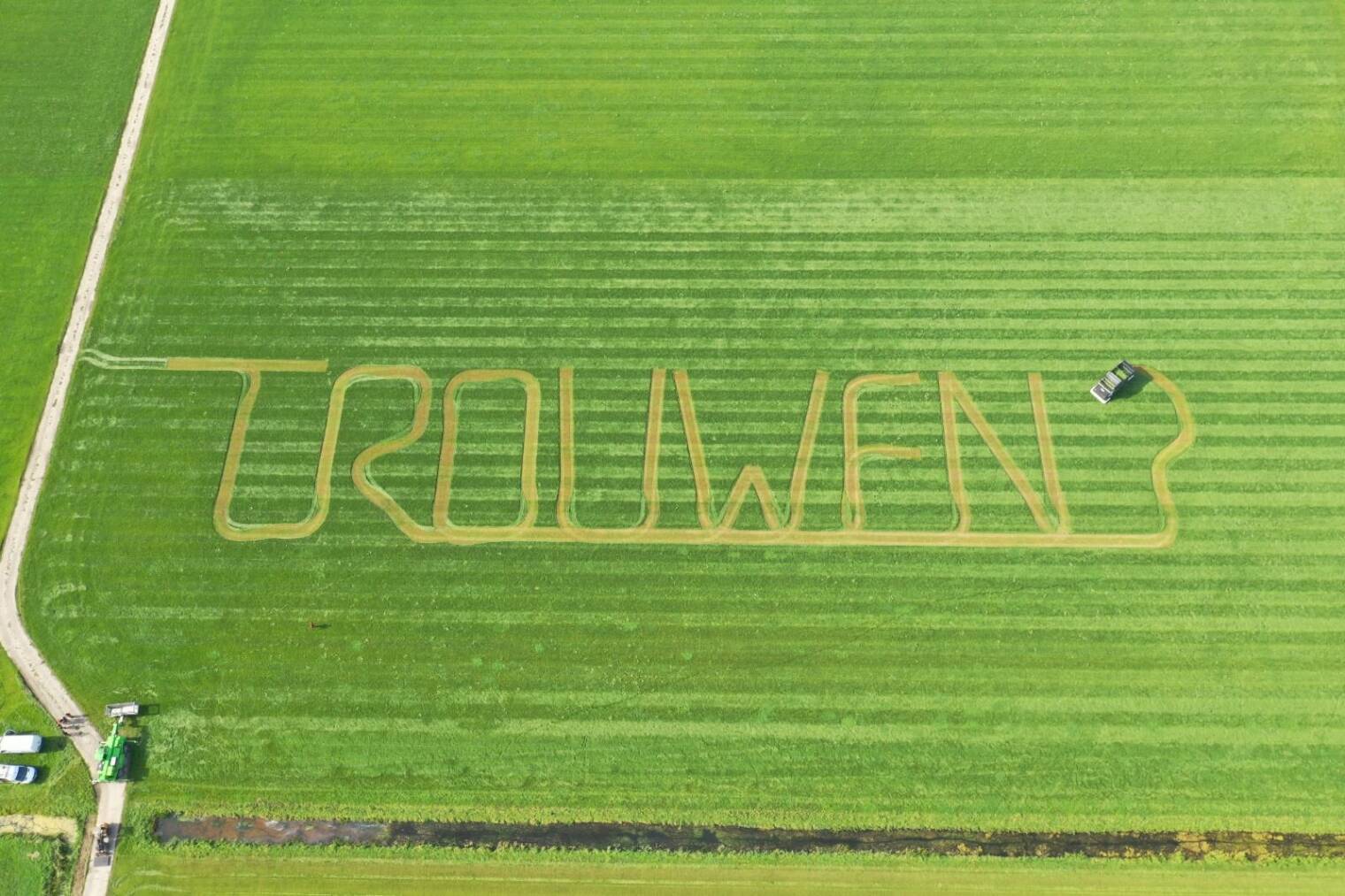
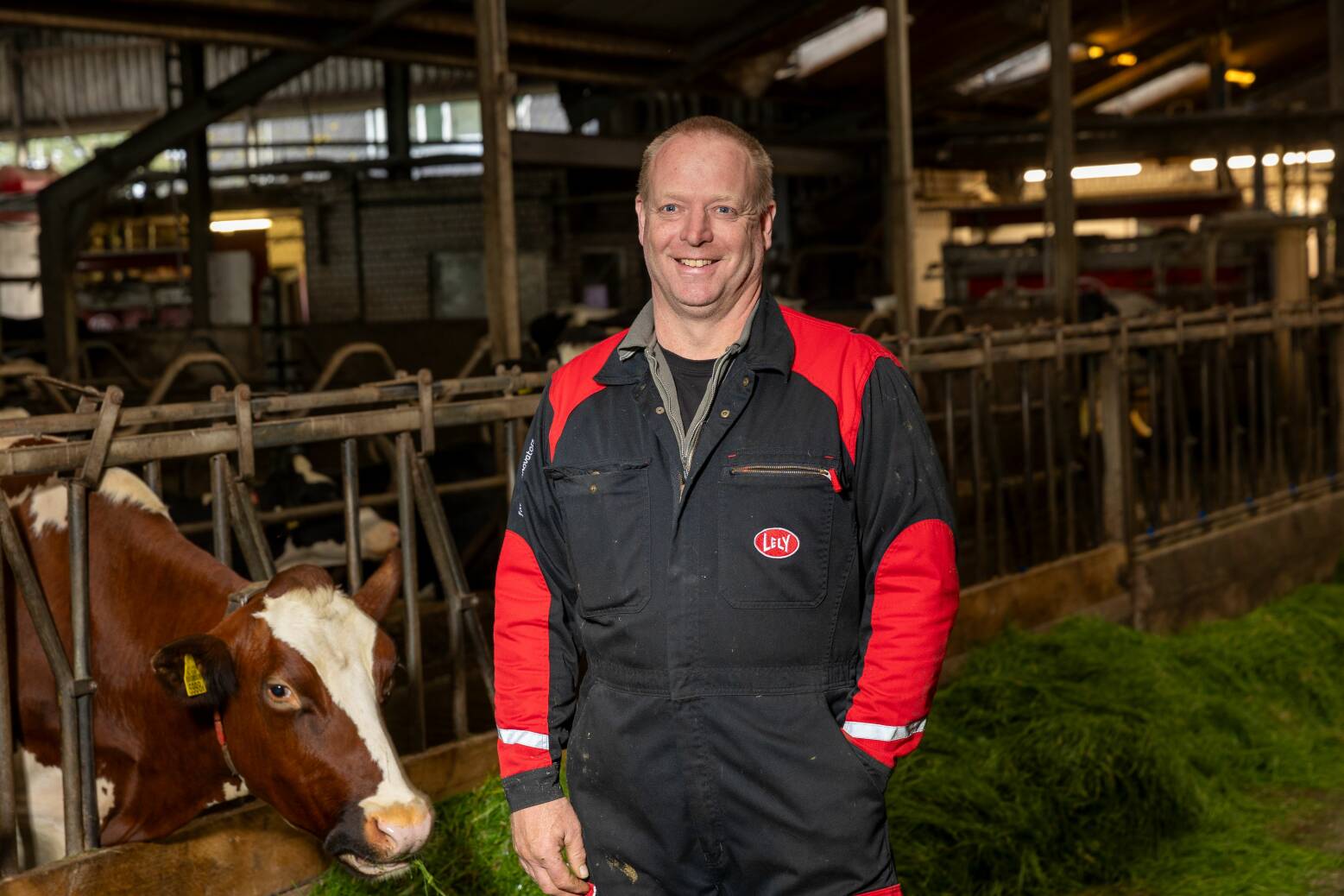
Peter recently proposed to Margo by using the Lely Exos to write the text ‘Trouwen?’ (‘Will you marry me?’) in a field.
Farm facts
Farm date: 1984 (at the current location in Terheijden)
Farm name: Van Oosterhout
Type: Family-owned dairy farm
Location: Terheijden, the Netherlands
Start date: 2012
Number of cows: 150
Lely robots: Lely Astronaut (3), Discovery Collector, Exos, Calm, Juno, Horizon and the Sphere
Lely Center: direct contact with Lely engineers
How did you become a Lely test farm?
Peter: ‘My parents moved to the current location in 1984, but there was no automation of any kind on the farm until 2010.’ Margo: ‘In 2012, Peter invested in our first Lely milking robot.’ Peter: ‘Our involvement increased over the years, and nowadays you can find all of Lely’s products on our farm, except for the Lely Vector.’ Margo: ‘Three years ago, we saw Lely’s appeal on Facebook for a farm to validate the Lely Sphere. During the process to become a test farm, we were asked by Farm Management to help them test Horizon.’ Peter: ‘And then they suggested that we could help with the Lely Exos as well, so we did. I’ve learned more in the last two years than in the ten years before that. I’ve also been pleasantly surprised to discover that being a test farmer takes up more time than I originally thought.’
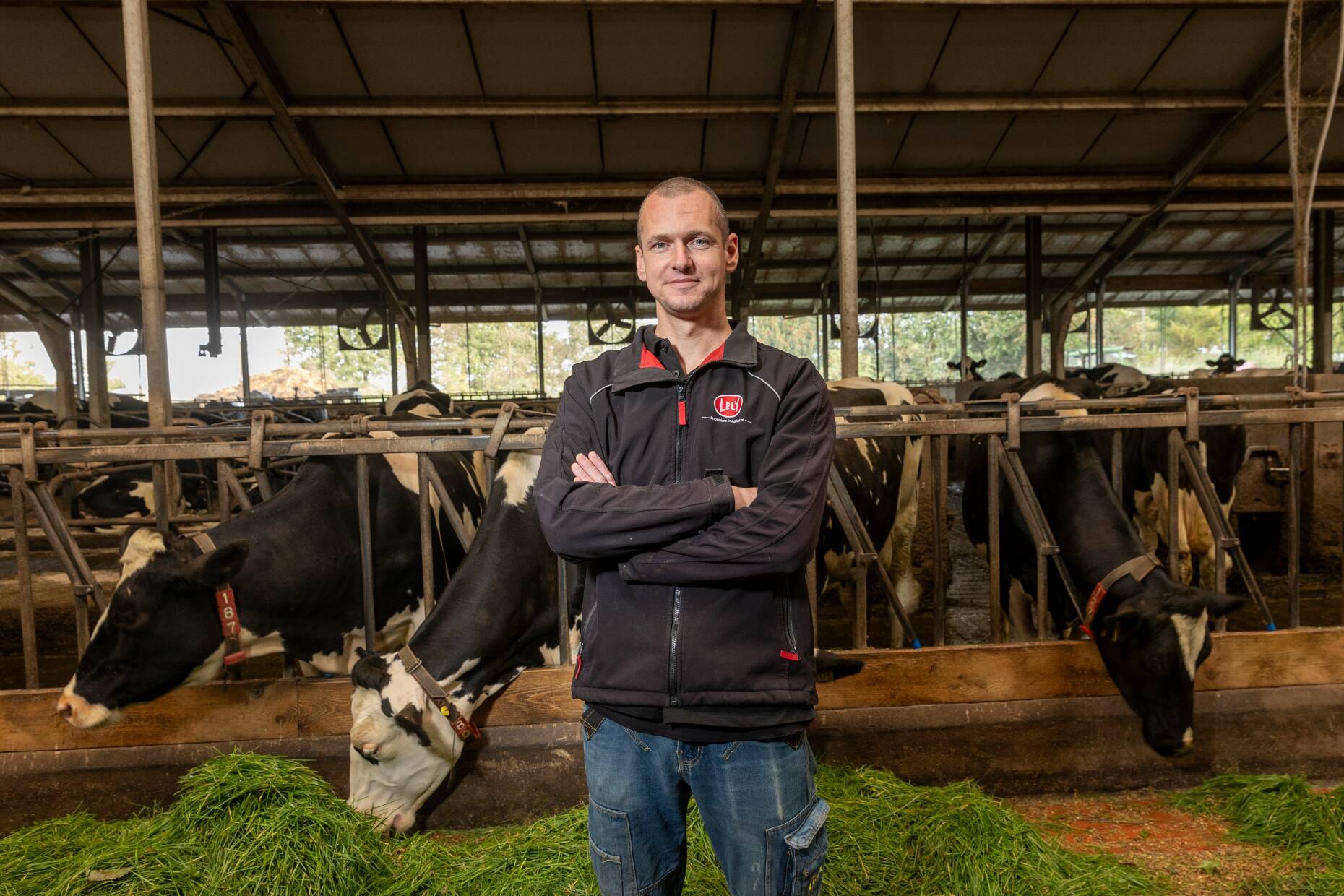
Ruud Aarts (43)
Test & Service Engineer
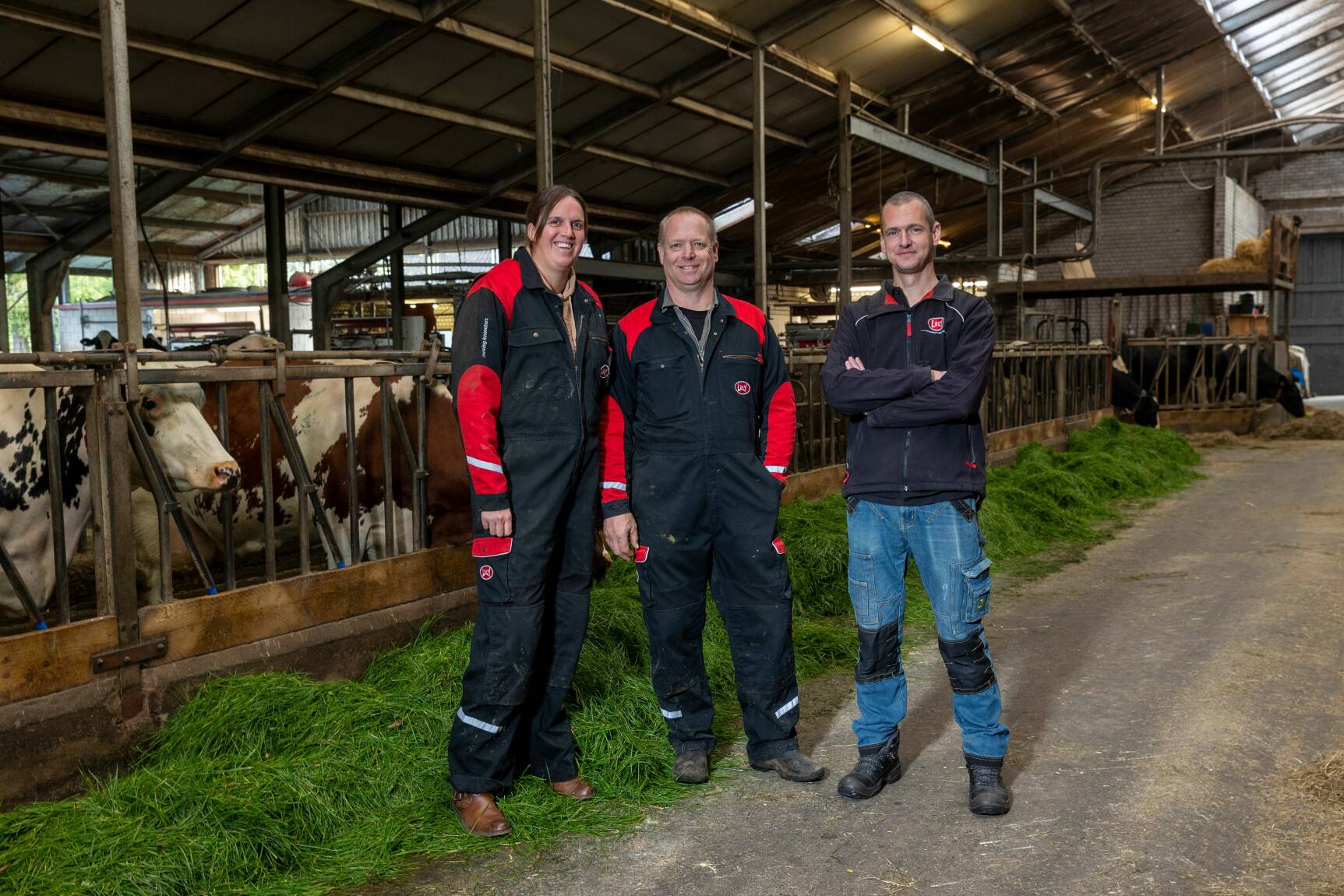
Margo (38) and Peter (50) van Oosterhout
Owners dairy farm
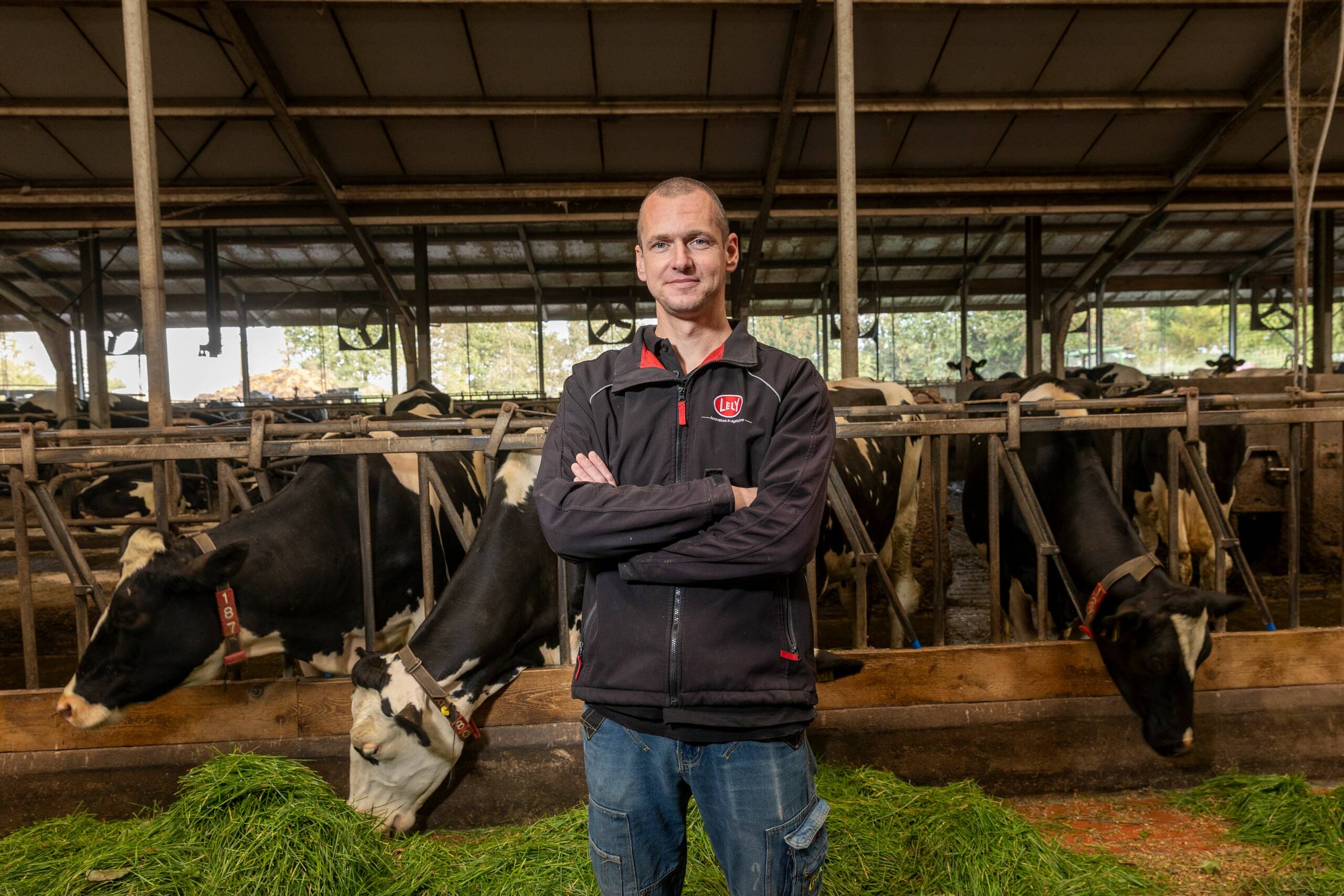
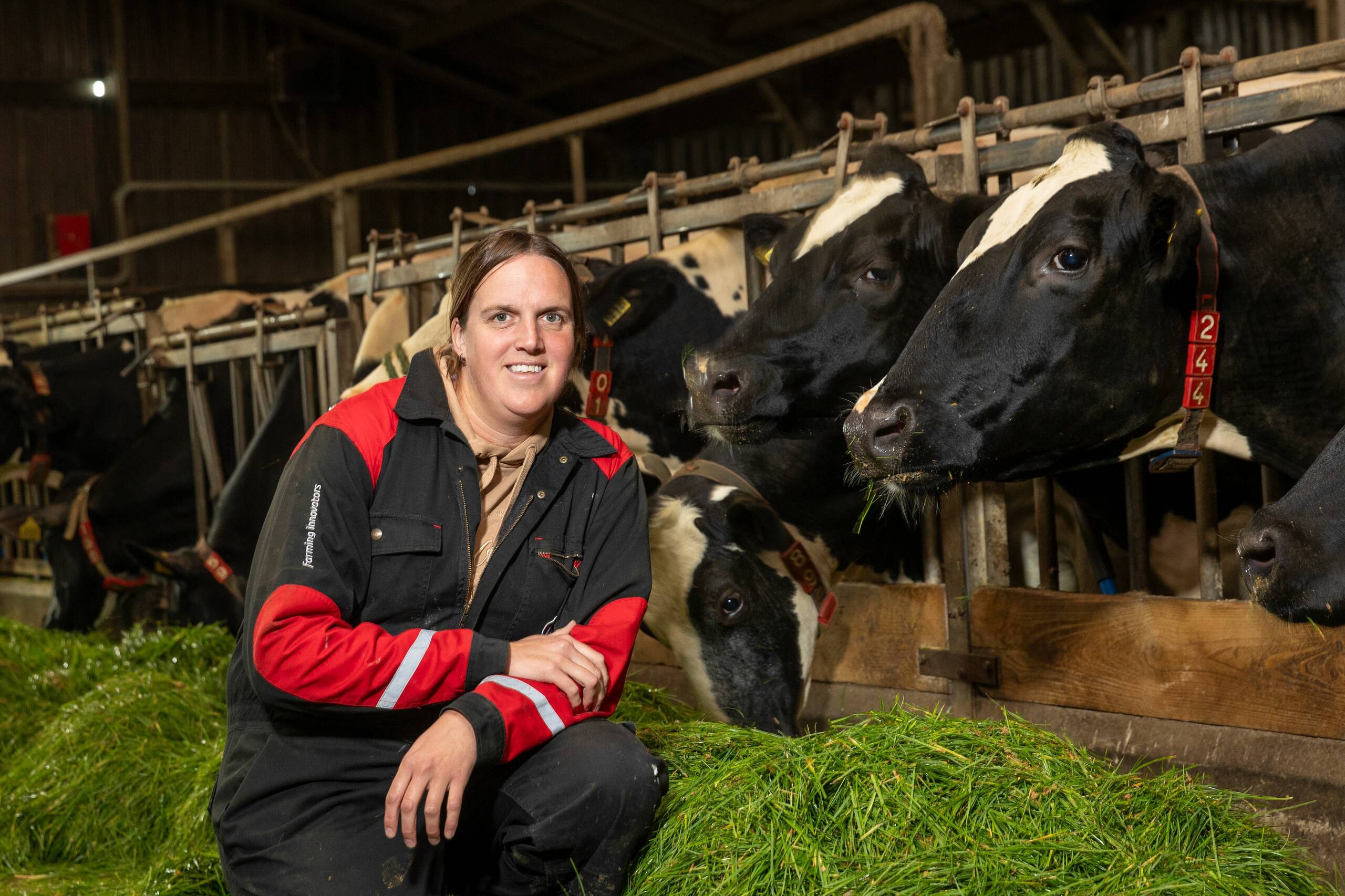
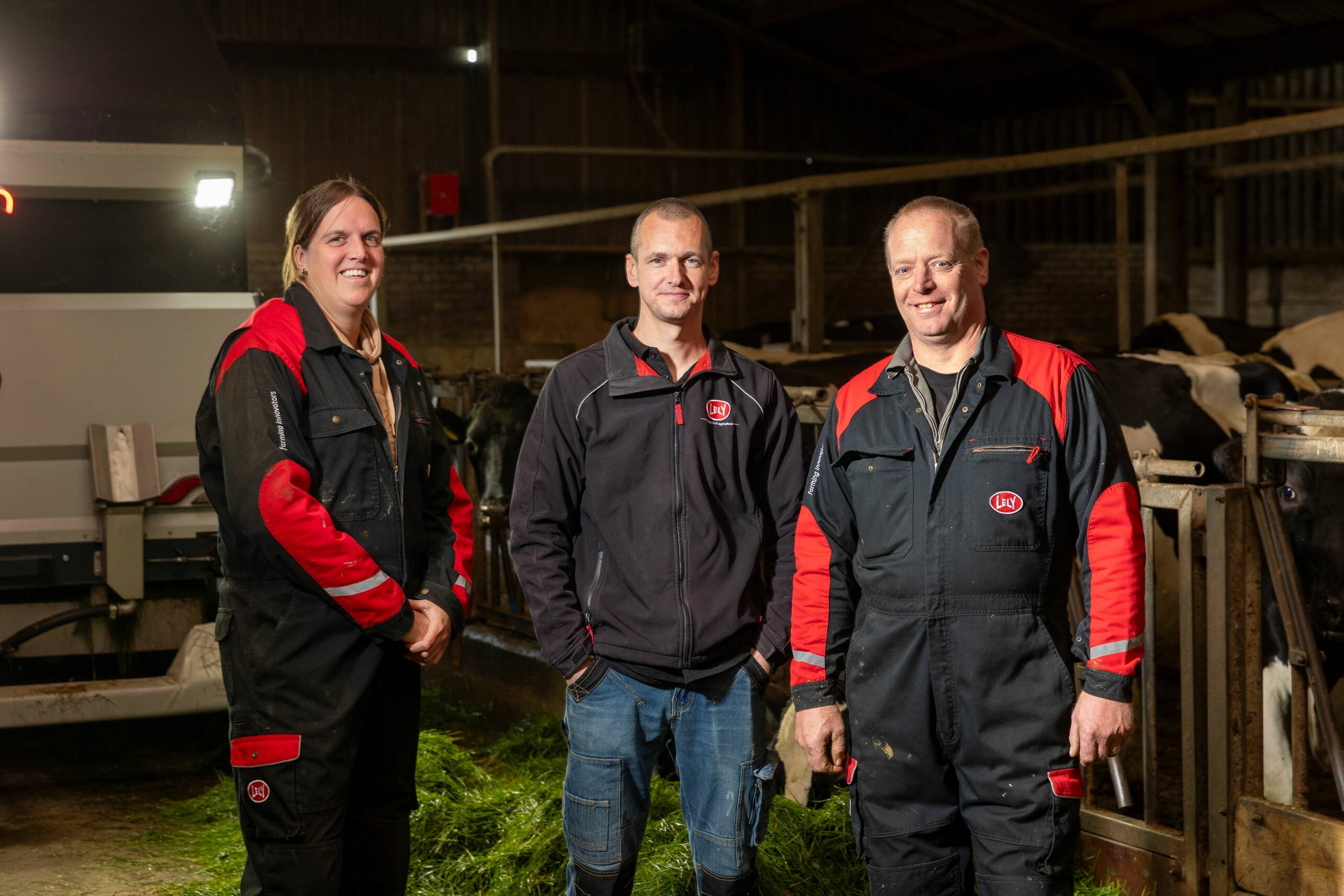
HAPPY FARMER
Peter van Oosterhout and his fiancée Margo took over the family farm in Terheijden, the Netherlands, five years ago. Today, the farm has been in the family for at least four generations. In view of Peter’s never-ending interest in technology, it was only a matter of time before the Van Oosterhout farm became a test farm for Lely’s innovations.
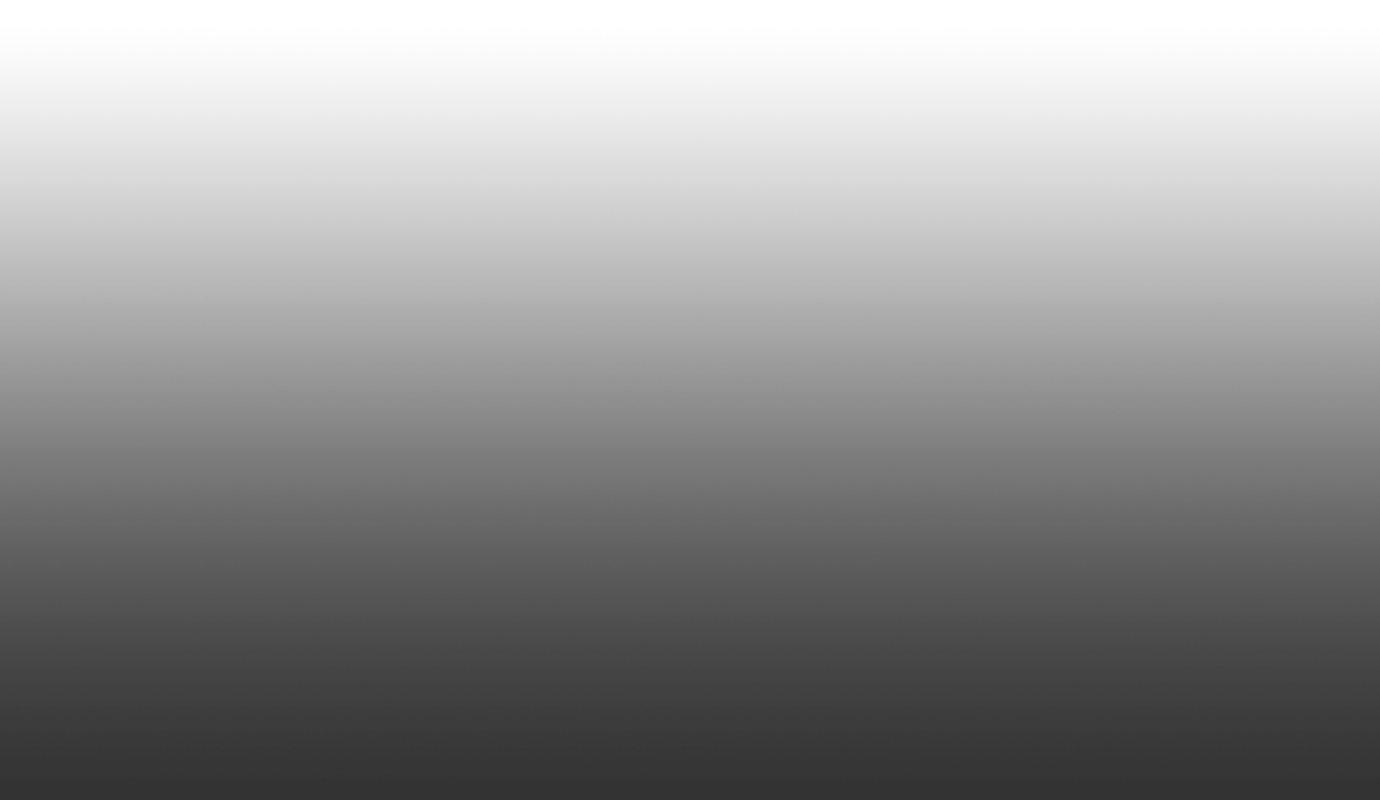
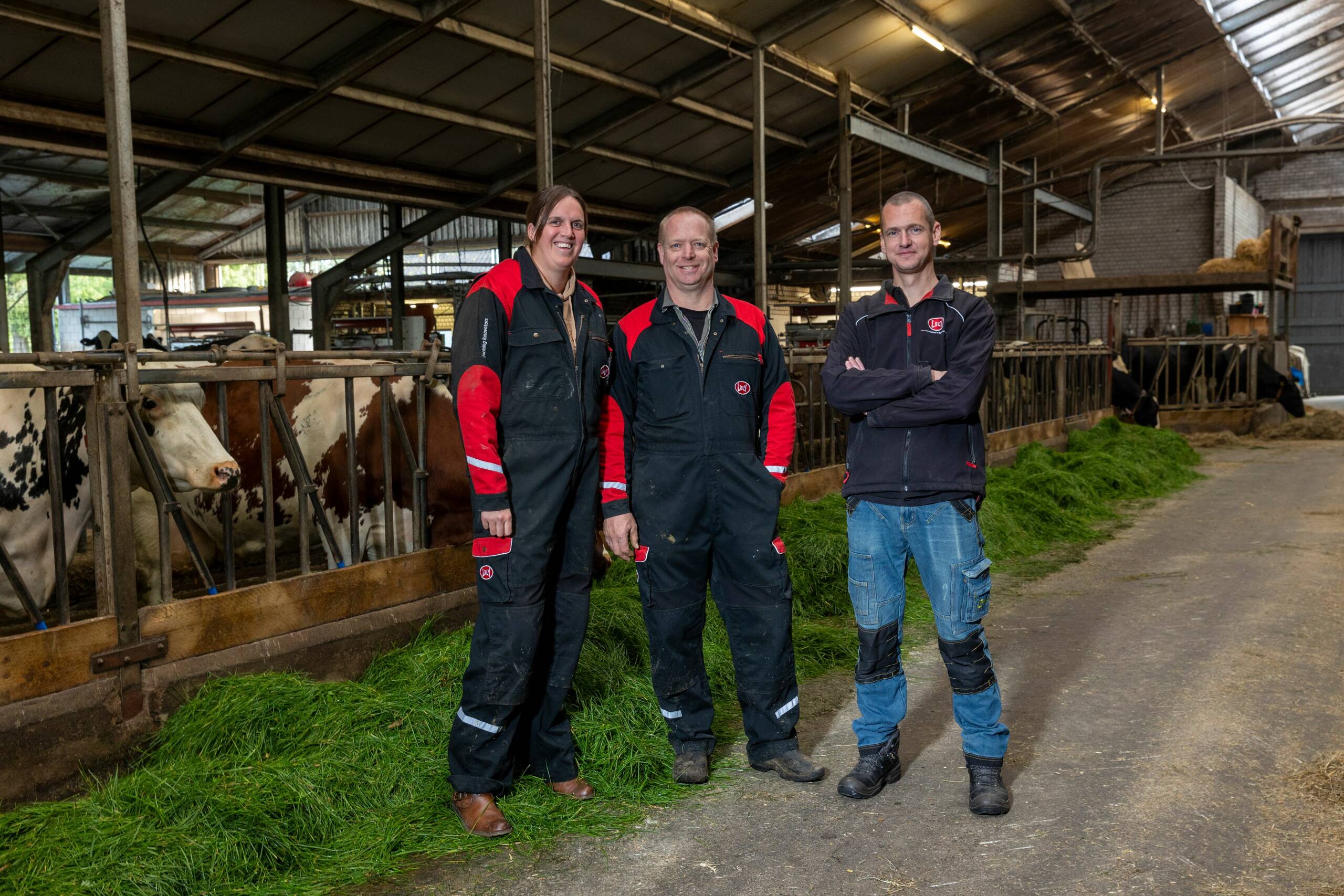
Peter recently proposed to Margo by using the Lely Exos to write the text ‘Trouwen?’ (‘Will you marry me?’) in a field.
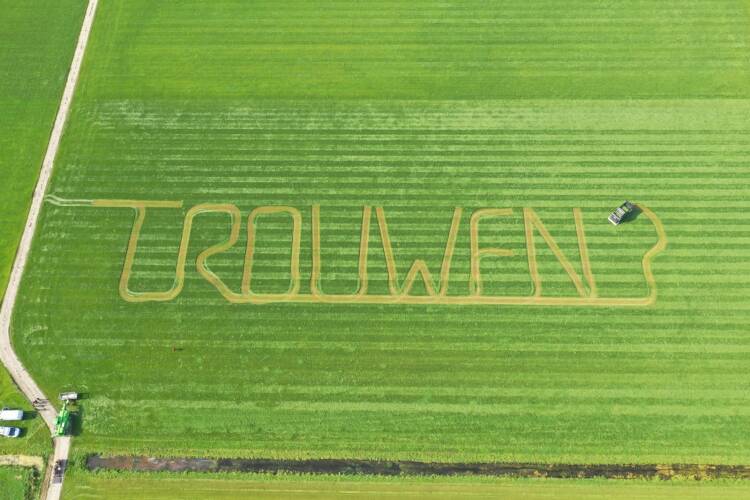
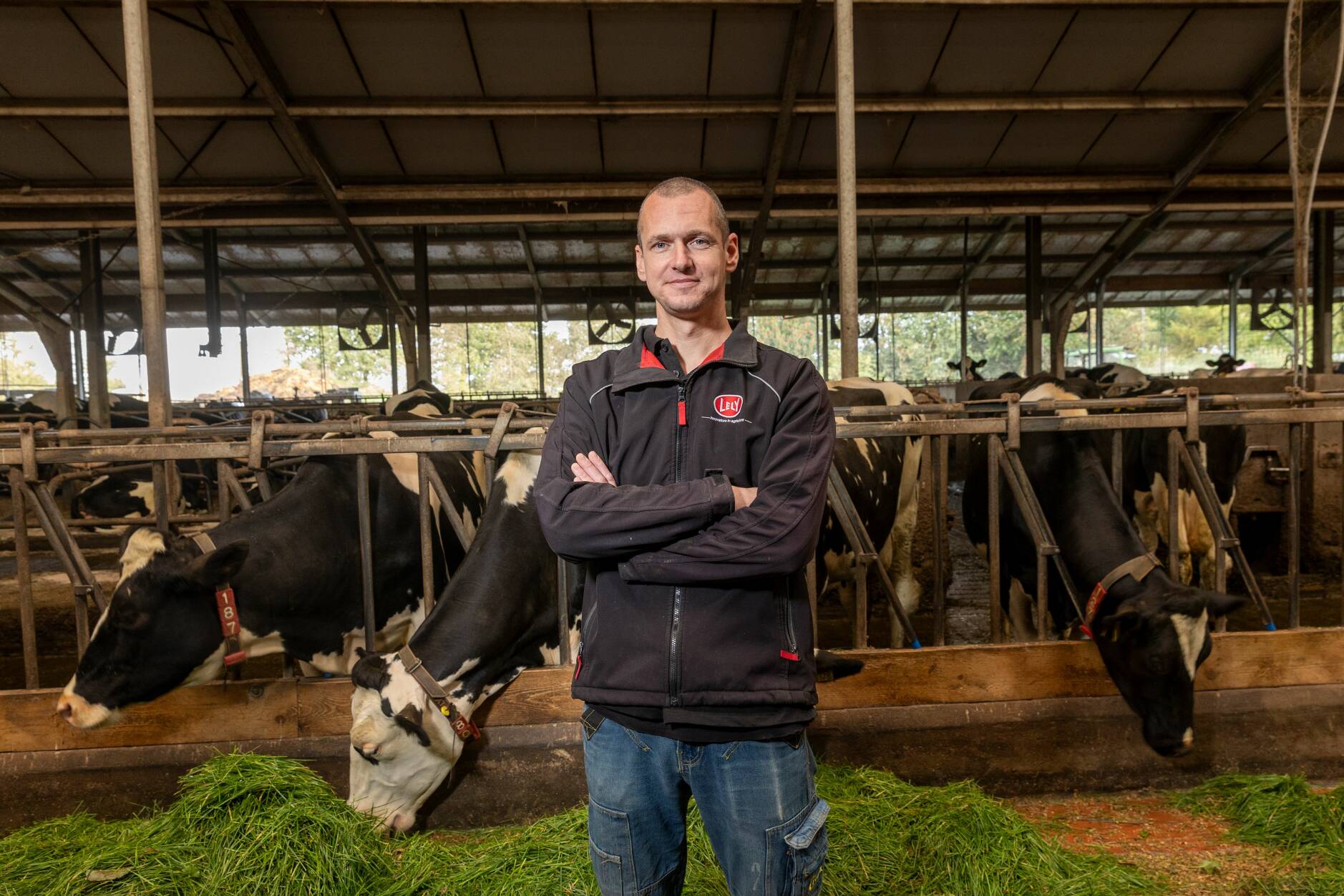
Ruud Aarts (43)
Test & Service Engineer
Ruud: ‘As a Test & Service Engineer, I bridge the gap between the farmer and the engineers at the office. Peter and Margo can call me if something is wrong, and I make sure the engineers receive this feedback. I also represent the service engineers worldwide. I give feedback on whether a product is easy to service, when commercially released. I have the most diverse job within Lely, I think! One day I will be doing maintenance or solving disruptions, the next day I might be pouring concrete at a farm, I tackle IT tasks, I do the planning for our department and I work on new ideas. I’ve been visiting Peter and Margo’s farm for a few years now. They are friendly and enthusiastic. Peter is really interested in the technology, which is important. He’s also very motivated, so their contribution is very valuable to us.’
Peter: ‘Whenever I call, I know my information will be passed on within Lely, and I always get feedback on what they did with my input. That’s crucial in a relationship with a test farm. I like improving things; when everything is running smoothly, I get bored.’
What is your role on the farm of Peter and Margo?
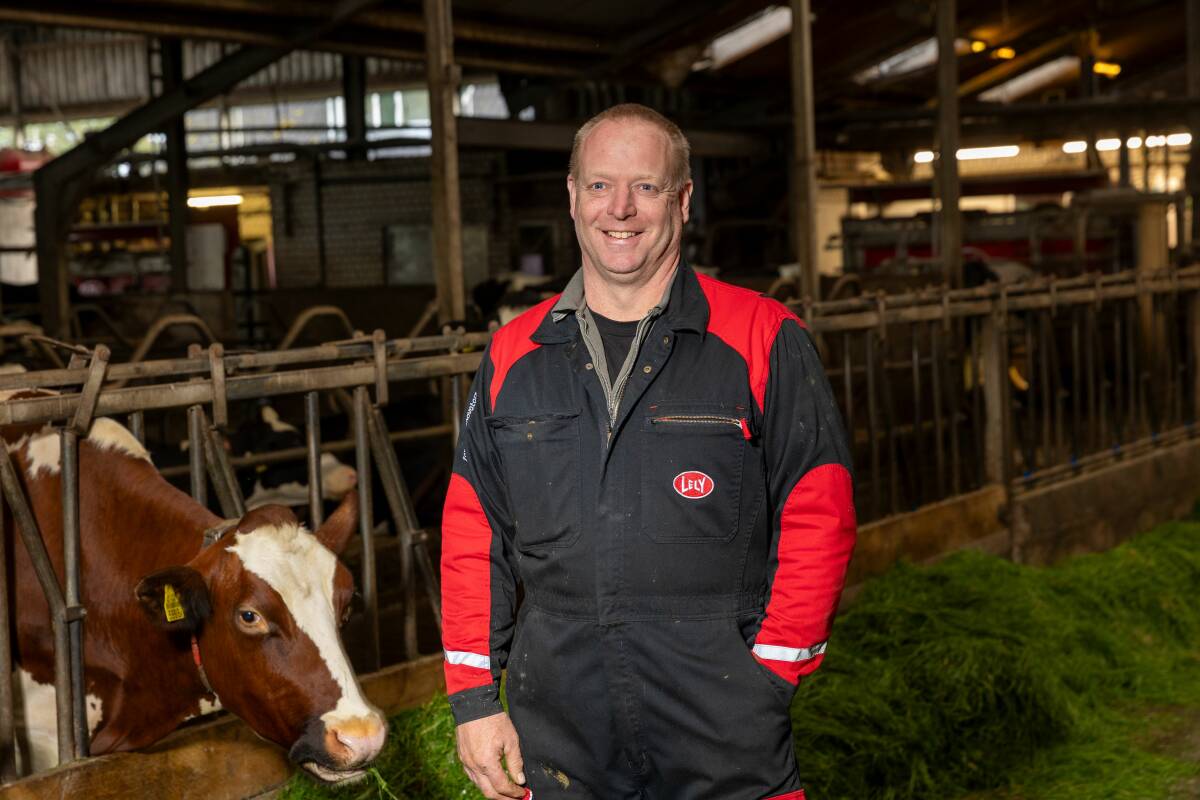
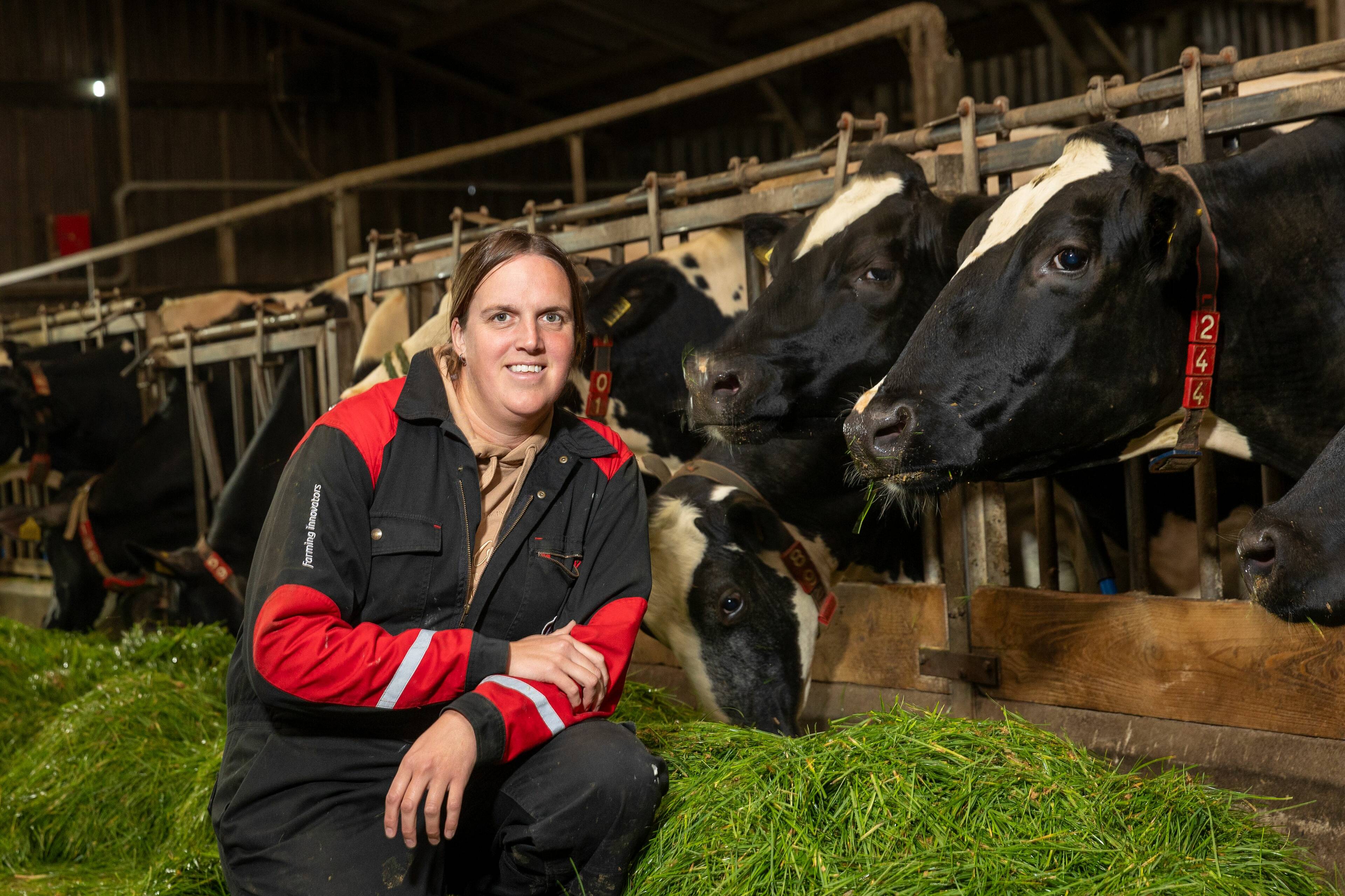
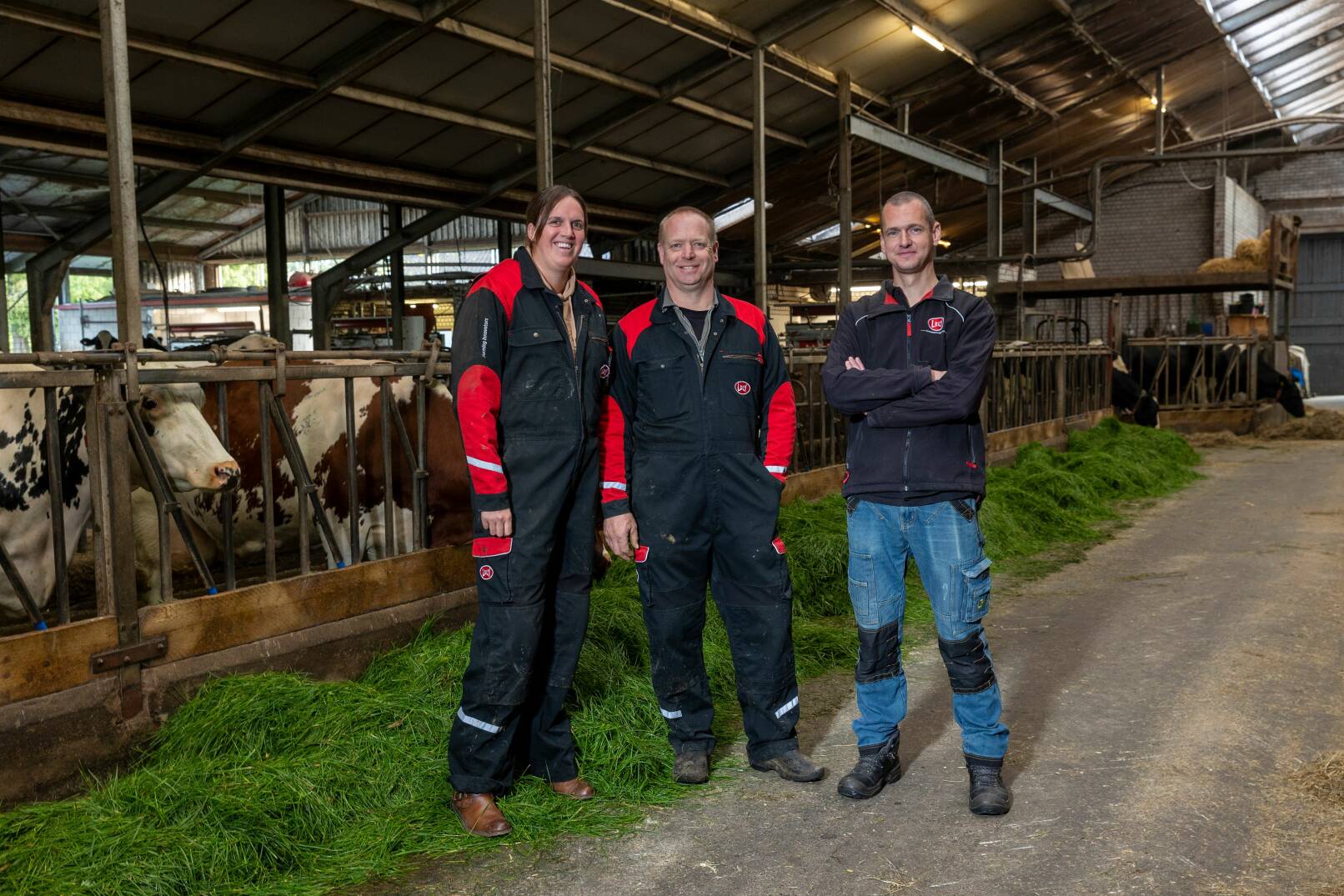
Margo (38) and Peter (50) van Oosterhout
Owners dairy farm
How did you become a Lely test farm?
Peter: ‘My parents moved to the current location in 1984, but there was no automation of any kind on the farm until 2010.’ Margo: ‘In 2012, Peter invested in our first Lely milking robot.’ Peter: ‘Our involvement increased over the years, and nowadays you can find all of Lely’s products on our farm, except for the Lely Vector.’ Margo: ‘Three years ago, we saw Lely’s appeal on Facebook for a farm to validate the Lely Sphere. During the process to become a test farm, we were asked by Farm Management to help them test Horizon.’ Peter: ‘And then they suggested that we could help with the Lely Exos as well, so we did. I’ve learned more in the last two years than in the ten years before that. I’ve also been pleasantly surprised to discover that being a test farmer takes up more time than I originally thought.’
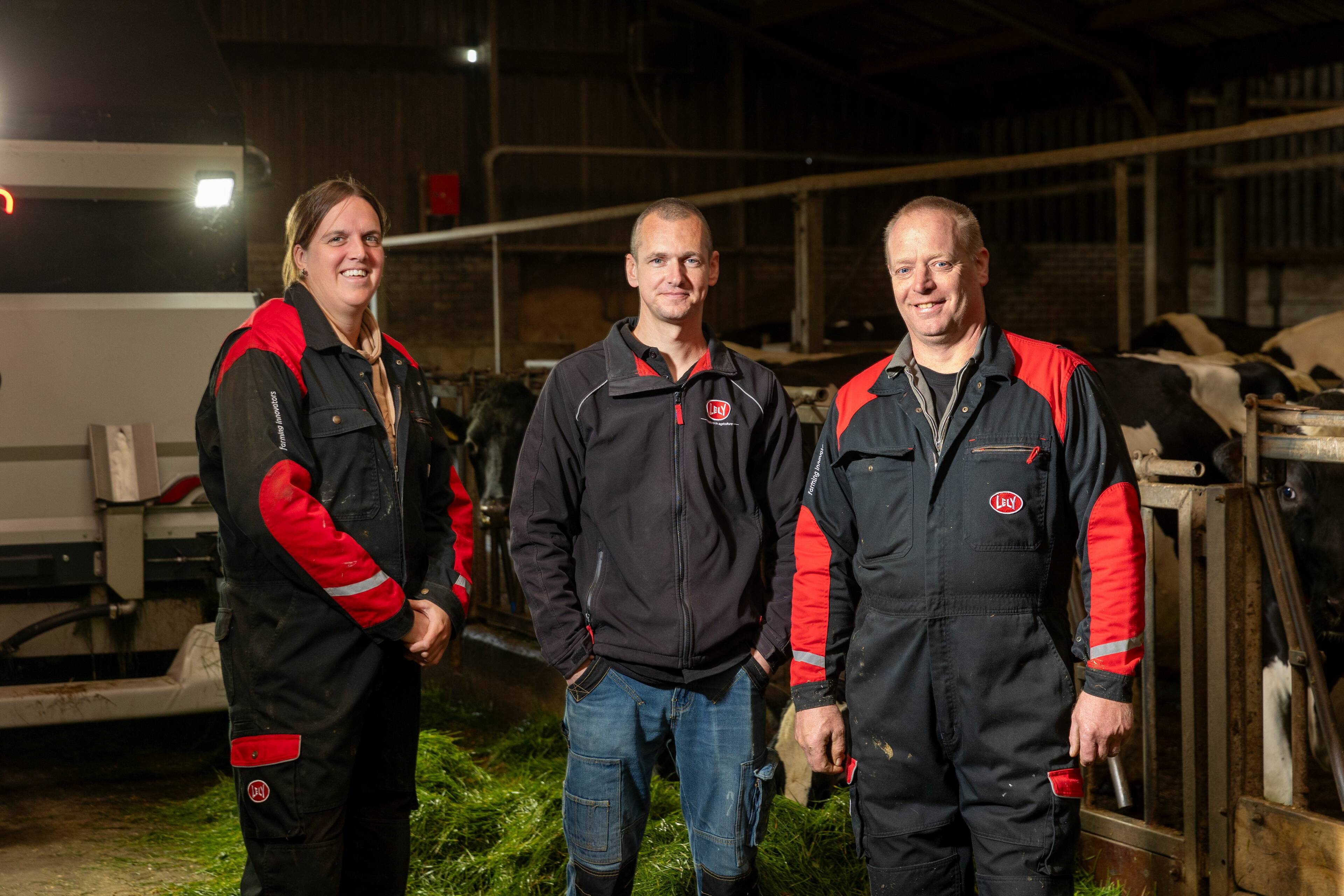
Peter: ‘Of course it’s on our minds. After all, we all get things like phishing messages. But I’ve been giving it more thought recently since my insurance company called and mentioned this subject. It made me realise that criminals can do malicious things that can shut your whole company down. I immediately called Ronald Pieterse, who handles IT matters for our farm. Ruud: ‘I used to find it a little annoying that you had to go through several verification steps before you could log in to our system. But now you hear about so many companies getting attacked. So you understand how important it is, and you learn to appreciate the verification procedure.’
This magazine is about cyber security. Is the topic of cyber security on your mind in the context of your farm activities?
Cyber security of our robots and data management systems has the highest priority. We give advice to our customers on how to use the system best. For example: using the system only for business purposes and not for private purposes. Of course, the farmer also has a responsibility in securing his or her data.
Peter: ‘As a test farm, you work with the Lely engineers much more intensively; you really get to know each other very well, including on a personal level. The whole relationship is built on trust. I know I can reach out to them whenever a disruption occurs, day or night. The Lely Industries team are so involved with their product and have such a huge sense of responsibility that they never mind. I have never seen employees so committed to their work; Lely should really cherish those people. And as a test farmer, you have to be committed too, and always alert. Disruptions can occur regularly, even in the middle of the night, and you have to take photos or film the alarm. Then, you have to log what you did to solve the issue. You suggest improvements and report malfunctions. If one engineer says it’s not possible to fix something, you need to convince them of the need for it to work. Eventually, there’s always an engineer who manages to find a solution. And the moment when something finally works properly is very fulfilling.’
Ruud Aarts, one of the Lely Test Engineers and working closely with Peter and Margo: ‘Remember that a lot of today’s engineers don’t actually have an agricultural background. Our farmers are their eyes and ears for the development work being done in the office.’
What’s the difference between being a Lely customer and being a Lely test farm?
Farm facts
Farm date: 1984 (at the current location in Terheijden)
Farm name: Van Oosterhout
Type: Family-owned dairy farm
Location: Terheijden, the Netherlands
Start date: 2012
Number of cows: 150
Lely robots: Lely Astronaut (3), Discovery Collector, Exos, Calm, Juno, Horizon and the Sphere
Lely Center: direct contact with Lely engineers
Peter van Oosterhout and his fiancée Margo took over the family farm in Terheijden, the Netherlands, five years ago. Today, the farm has been in the family for at least four generations. In view of Peter’s never-ending interest in technology, it was only a matter of time before the Van Oosterhout farm became a test farm for Lely’s innovations.
I get bored’
HAPPY FARMER
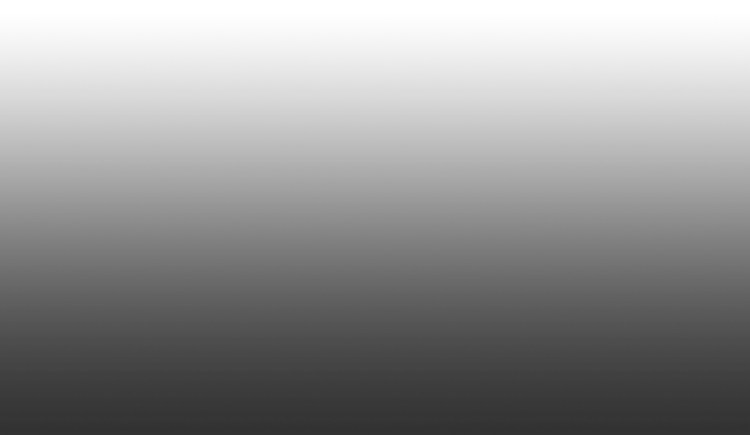
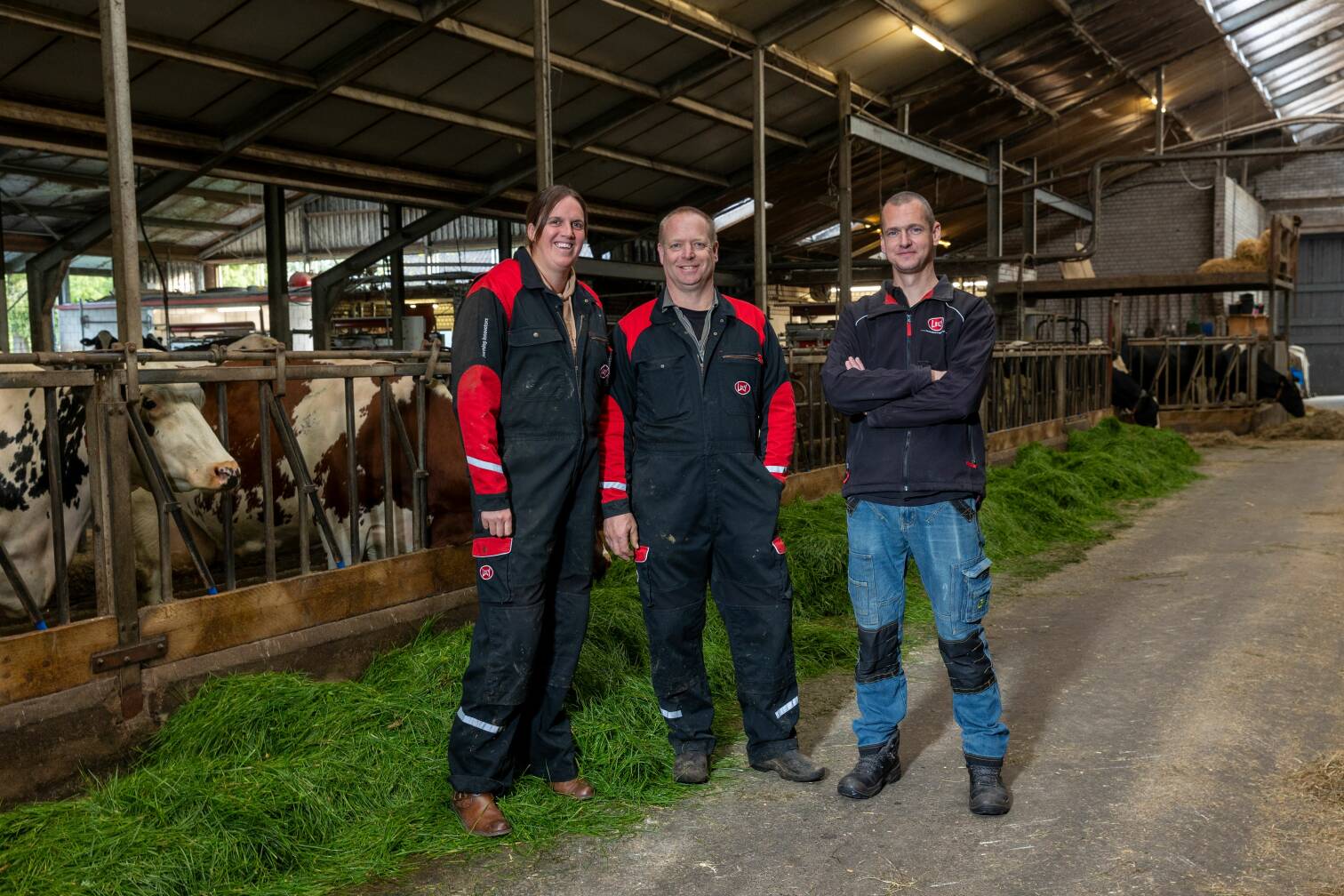